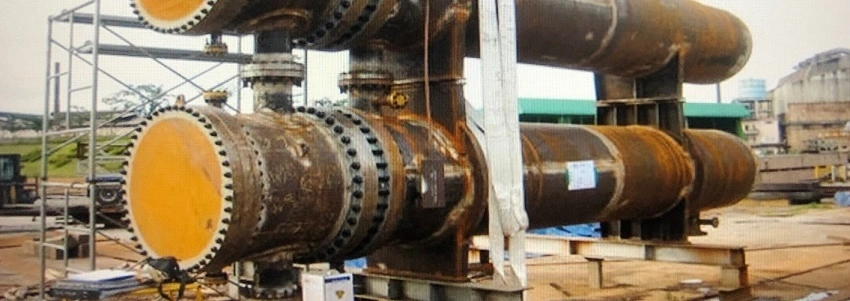
He remembered what his Level III Instructor had told him repeatedly while he was completing his training as a Level II NDE Technician a year ago. "What you do is important", he had said. "Don't ever get complacent and think that what you do doesn't matter", he said. Well, after going from one job to another at various client facilities during the last year it became quite clear that his job was a routine run-of-the-mill job. No great mysteries were uncovered by his day-to-day UT readings. He handed his UT reports over to his API Inspector and it was funneled up through the client's program. Nothing extraordinary there. Then one day he found something that made him realize just how true those words were from his Level III Instructor.
A brand new FCCU was being built. The ground throughout the unit was all still sand/dirt/rock but the regenerator, stripper and reactor were up. Most of the columns were up, drums were set, banks of exchangers were being stacked in. Structural steel platforms were set or being attached and the piperacks were all up throughout the unit although not much pipe was laid in them yet. Construction contractor workers were crawling everywhere. It strongly resembled a freshly kicked ant pile.
Into this seemingly madhouse of activity strolled a young contractor NDE Technician with the assignment to take baseline UT readings on as much of the fixed equipment that he could reach from the ground or from his 20 ft extension ladder. After a few days of strange looks from the 2 or 3 Contractor Construction Project Managers (Goldhats for some of the older generation) snide remarks were made asking if the young NDE Tech had found any thinning or corrosion. Oh, they all had a good laugh. Their faithful entourage of 5 or 6 Superintendents and General Foremen seemingly laughed a little extra for the benefit of their superiors. One old GF didn't - he just nodded.
This bank of FCCU Bottoms Exchangers were shell & tube type and were stacked three high. They were big (maybe 48" or so) had 1.5" or 2" bolts on the heads and somewhere around 20-24 feet long. Sorry, don't remember exact pressure or temperature but it was FCCU Bottoms so that should give a hint. The nominal shell thickness was 1/2" or 5/8" (long time ago). UT reading were being taken at the typical locations of top, bot and N, S, E or W at both ends and in the middle. Usual routine stuff.
All was going well with readings at or slightly above nominal. Then on the bottom exchanger on the bottom side shell it hit a reading around .350" or so. Tried again and got the same range. Moved over a few inches to the right and it was the same. Calibrated machine and repeated. All same. Moved other direction and after moving over 6-8" to the left it got back up to the nominal range again. After dozens of readings later, and outlining the area with metal marker, the bottom side of the bottom exchanger shell had a 2 ft by 3 ft area of readings from .250" to .400". It looked like a map of the African continent in reverse.
The client Chief Inspector was notified and immediately came out. He had been in the business a couple decades, and after he confirmed readings with his machine, he called out his Supervisor and the Project Engineers. With all the Client big shots gathered around and discussing the ramifications (destruction and death) of a possible lamination in the brand-new shell it couldn't help but attract the Goldhats and their entourage. The young NDE Tech just stood on the fringe for a little while as the clients were instructing the Contractor to prepare to pull the exchanger and return it to the fabricator. As the young Tech started to walk away to go to the next vessel on his list, he heard a voice, "Hey, Technician." When he turned to look, the entire group was looking at him. The old Construction General Foreman (not one of the Goldhats, of course) said, "Well done, son", and tipped his hardhat. The older Chief Inspector had a slight grin and nodded too.
It was a good day.
Case Study Inquiry